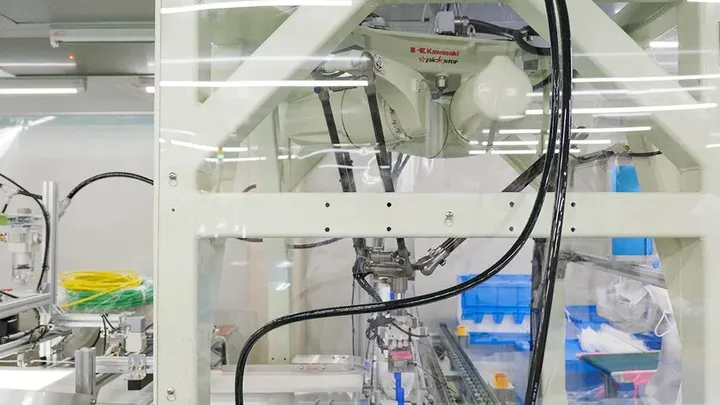
- IndustriesMedical
- ApplicationsMaterial Handling
- Robot SeriesYF series
Japanese machinery design group, SHOWA Corp. develops and sells commercial industrial washing machines. But they added something new to their product lineup when the COVID-19 pandemic began: mask production. In March 2020, they began manufacturing face masks to help alleviate the effects of the widespread PPE shortage. Less than a year later, sales from the mask business are second only to the company’s main line of cleaners. Kawasaki delta robots helped make that possible.
CHALLENGES
- Inefficient manual work yields defective product
- Company cannot meet production goals
Initially, their mask manufacturing process involved intensive manual work, resulting in long lead times and excessive in-process inventory. Moreover, there were frequent product defects. Though SHOWA’s initial production capacity was approximately 1.5 million masks per month, the number of orders exceeded 2 million per month. In order to meet the demand, their production process needed drastic upgrades.
SOLUTION
The in-depth mask production process includes many steps. The non-woven fabric must be cut, superimposed and creased. Nose-fit wires and ear straps must also be attached, and the entire mask must be inspected for defects with a camera. Then, they are wrapped individually in vinyl and packed in boxes.
To increase production capacity and minimize reliance on manual work, SHOWA needed to fully automate the production process. They wound up automating the entire mask manufacturing process, from inspection to packaging and packing for shipment.
RESULTS
- Kawasaki Y series pick and place robots run 24 hours a day
- Production increased from 1.5 million masks to 9 million masks per month
- Labor reduced significantly
Automating the entire process allowed SHOWA to drastically reduce the number of workers required for the process. They achieved a production capacity of 2 to 3 million masks per month. After making additional improvements, SHOWA can now produce more than 9 million masks per month.
Kawasaki’s high-speed Y series picking, or delta, robot runs 24 hours a day, which directly contributes to SHOWA’s impressive production. The company reduced the number of transporting staff from 10 to 1, further improving overall efficiency.
Y Series High-Speed Delta Robots
Pick and place, or delta, robots are widely used in the food, pharmaceutical, and electronics industries for their quick and accurate material handling capabilities. Their thin, long-reach arms are reminiscent of a claw machine game, giving them high agility, speed and accuracy capabilities.