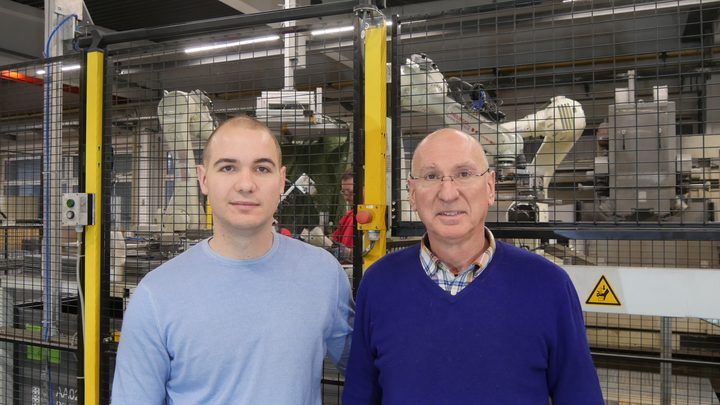
- IndustriesMachinery & Metal Manufacturing, Automotive
- ApplicationsMachine Tending
- Robot SeriesRS series
Hands-on sustainability and always close to the customer: Nuremberg-based special machine manufacturer relies on Kawasaki robots for precise and economical automation of production processes.
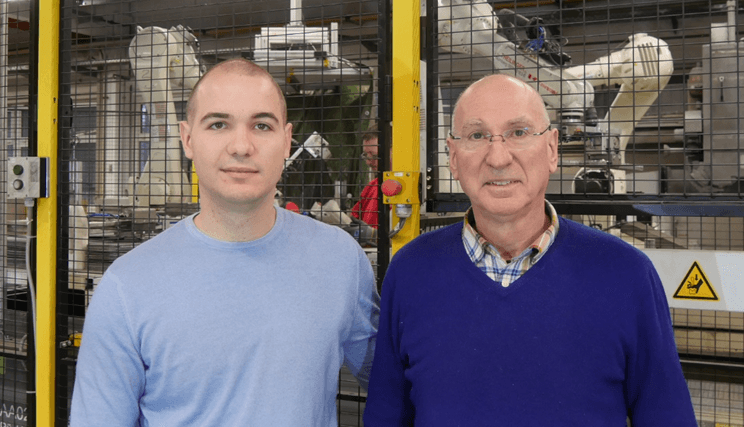
An industry in transition: German automotive suppliers are currently facing difficult challenges amid rising costs, overcapacity and high uncertainty. Theilinger has been close to the industry for 30 years and knows its needs inside out. With robots from Kawasaki Robotics, the Nuremberg-based company supports its customers with tailor-made automation, even in difficult times.
There are few standards; for company founder and owner Richard Meyer-Theilinger, custom-made products are the key to continued success: “Our company motto is ‘Do the right thing at the right time, in the right place’ and that means that every customer request, and therefore every order, offers the opportunity to take functionality to the highest level.”
Automation for Siemens, Schaeffler and ZF Friedrichshafen
Theilinger’s beginnings more than 30 years ago were already based on these customer requirements: Meyer-Theilinger was project manager for automation of ball bearing production at GMN in Nuremberg. After the automation division was discontinued in 1993 due to restructuring, Meyer-Theilinger was approached directly by former GMN customers for his services as an engineering office – including existing customers such as Schaeffler, ZF Friedrichshafen and Siemens. In addition to planning, there was a growing demand from customers for a comprehensive range of services – which he built up over the next two years, including production.
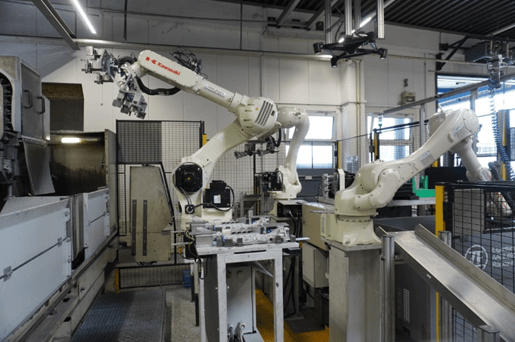
Today, 25 employees work at Theilinger on the development, design and production of turnkey automation solutions – with a focus on automated handling solutions. The company places particular emphasis on innovative concepts and the development of new areas of application. Here, the focus is particularly on bin picking – an advanced solution in which robots use highly developed image processing technology to precisely remove unsorted parts (bulk goods) from containers and optimally feed them into the subsequent production process. Bin picking with reliable quality detection is the specialty of the Nuremberg-based special machine builders. Three programmers are currently working on the development of robot and software solutions, while three other experts specialize in PLC programming for conveyor and machine control systems. Image processing is a key topic for the future, which Theilinger has already successfully implemented in numerous projects and demonstrates in videos on its website. Due to increasing demand, a wide range of applications, falling prices and growing user-friendliness, Theilinger is increasingly focusing on the further development and integration of such systems, which have already proven themselves in practice many times over.
Cooperation with Kawasaki Robotics
Relationships with suppliers and partners are maintained on a very long-term basis. Richard Meyer-Theilinger and his team always stay close to the market and are open to new and better solutions. This is how the collaboration with Kawasaki Robotics began over 12 years ago: A mutual customer opted for Kawasaki robots and Meyer-Theilinger was quickly convinced: “The technology and cost-effectiveness was noticeably better than anything else on the market and immediately appealed to us.“ Since then, we have successfully completed numerous projects together with Kawasaki Robotics and now use Kawasaki robots as standard in our projects.”
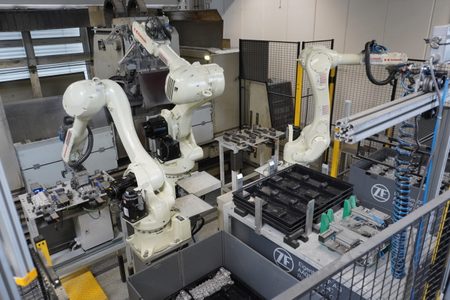
In the last two years alone, Theilinger has integrated 22 Kawasaki robots – including for demanding sorting tasks such as universal joints in propeller shaft production for commercial vehicles. A further 11 robots from the Japanese manufacturer have been ordered for the massive conversion and expansion of an automation system in 2025. The complex task involves the precise removal, testing, sorting, milling and lasering of numerous different parts. Philipp Theilinger welcomes this challenge: “It’s demanding, but we’ve mastered it. We have respect for the task, but we know how to master it – and we rely on the proven quality of Kawasaki robots”.
Extremely cost-efficient for customers: Among other things, Theilinger buys used milling machines at low prices and subjects them to a comprehensive retrofit. Spare parts are also reconditioned and reused sustainably. For Theilinger, it goes without saying that the cost savings are passed on directly to the customer: “We have the expertise and the means to stay well below the usual price. This is a huge cost advantage for our customers and more important than ever in times when every investment is under scrutiny.” The company building in the north-east of Nuremberg also continues the company philosophy: the entire roof has been equipped with photovoltaic systems for years and easily covers the energy requirements of the building and production on clear days – and usually even feeds green electricity into the grid.
Kawasaki robots produce new generation of transmission control parts
Two newly commissioned processing lines, each with three Kawasaki robots from the RS series, are working at full speed at Theilinger for long-standing customers in the automotive industry. The RS020N models perform automated removal using bin picking, supported by a camera system that enables precise sorting and provision of the parts. In addition, the processing quality is finally checked using AI-supported image processing. An RS030N is also used for loading the CNC milling machine. The high-speed robots in the RS series are true all-rounders: with their compact design, flexible working range, long reach and maximum precision, they are suitable for a wide range of industrial applications.
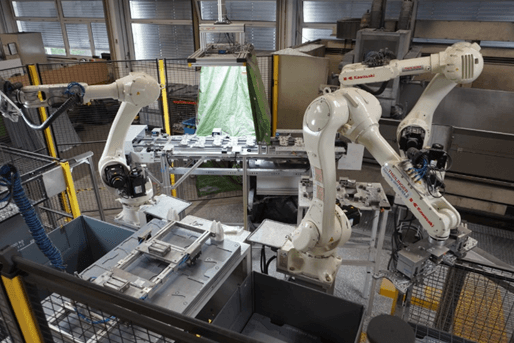
The systems are extremely efficient and well thought out down to the last detail: the cycle times of all robots and process steps are optimally coordinated. Both RS020N robots alternate when using the large gripper for several parts – automatic and fast tool change included. In addition to maximum efficiency, maximum precision and quality are crucial in this project: each system produces thousands of components every day with a minimum error rate, reliably meeting the high requirements of the automotive industry. Another important plus in times of strongly fluctuating capacities: Production is easily scalable. An output of 10,000 units per day could be implemented immediately if required. The capacity could even be increased to up to 20,000 per day. The systems are extremely efficient and well thought out down to the last detail: the cycle times of all robots and process steps are optimally coordinated. Both RS020N robots alternate when using the large gripper for several parts – automatic and fast tool change included.
Outlook: Securing the future of production through automation
Theilinger will continue to focus on automation solutions in the coming years. In addition to the automotive supply industry, other sectors are increasingly being added – including the construction industry, fastening elements in joining processes, heating construction, screw elements in machine tools and lathes and many more. Regular maintenance is essential – this is how downtimes can be reliably avoided and minimized. In addition, the Collision Detect option for the Kawasaki Robotics Controller is used as standard to reliably prevent damage during operation.
Richard Meyer-Theilinger is convinced that monotonous and physically demanding tasks such as handling components are neither economical nor practical for the use of human labor in the long term. Such tasks not only impair production reliability, but also make it more difficult to plan and increase the efficiency of the entire operation. “Kawasaki robots offer an extremely economical and reliable solution here,” explains Meyer-Theilinger. “By combining them with modern camera systems, sophisticated automation concepts and our comprehensive expertise, they secure the future of almost any production environment.”